Within the overlapping spheres of Total Quality Management and Lean Manufacturing, one Japanese word continues…
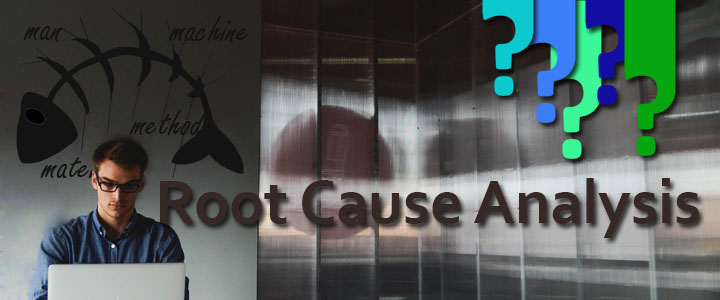
When Should Root Cause Analysis be Performed
When problems arise in the process, the knee-jerk reaction is often packaged two-fold: (1) solve the problem, and (2) blame the culprit, the one responsible for subverting the process status quo. While we cannot stress enough the value of being responsive to critical incidents and holding people accountable for their actions, organizationally, we don’t want a culture where people repetitively solve the same problems, and assign blame to someone just because it’s the easiest thing to do when investigation occurs.
THE EFFICIENCY TRAP
While every problematic situation or incident is an opportunity to improve, it’s important not to fall prey to the illusion of productivity and “being constantly busy” when solving these problems. Many people think that being successful in doing quick fixes already testify to their productivity and efficiency. Most of the time, what is applied are merely Band-Aid solutions – short-term and unsustainable.
To the uninitiated, the ability to solve problems – however preventable they are – is indicative of excellent employee performance. After all, isn’t “problem solving skills” one of the Trojan horse credentials that all too many employers and recruiters love to look for in potential employees?
HOLD YOUR HORSES!
Before we become so exorcised about solving a problem, there is another process we must undertake correctly to ensure that the solutions we will create are those for the true root cause of a problem. Again, each problem is an opportunity for improvement. It contains the information needed to eliminate the problem itself. For that we need ROOT CAUSE ANALYSIS, a collection of process, tools, and methods to identify what, how, and why something happened.
CLASSIFICATION OF “CAUSES” OF PROBLEMS
Process-wise, we can talk about “causes” of problems in two types: Common Causes or Special Causes.
- COMMON CAUSES
Common Causes are results normal process variations that affect the performance or quality of the output. To eliminate common causes, the process itself needs to be improved or refined.
To understand common causes better, let’s have an analogy: suppose your commute to work is a process. Apparently, the acceptable quality of output is that you “arrive to the office on time.” The question is: what are the common causes you are likely to encounter?
For some, the common causes that affect their arriving to office on time are the terminal queues, stoplight patterns, or traffic enforcer instructions. These are events that happen most of the time yet have little impact on the output. These things may affect your time of arrival to office but only by a few minutes. Short of saying, they still allow you to fall within the range of acceptable level of performance or quality.
- SPECIAL CAUSES
Special Causes are attributed to something outside the normal process, and which results to an abnormal process variation. Generally, special causes occur infrequently, but nevertheless have a tendency to recur.
Referencing the Commute to Work process above, possible special causes are, for example, vehicular collision, engine malfunction, or bad weather – incidents that cause huge impact to the process and the quality of output. They rarely occur, but the result is a process-gone-out-of-control.
WHEN TO PERFORM ROOT CAUSE ANALYSIS
Between the two, special causes are the best candidates for root cause analysis.
Of course, not all problems merit the rigors of Root Cause Analysis. Conversely, there are problems too big and too systemic in the organization which true root cause/s cannot be readily identified in just a few RCA sessions. But if we want to solve problems and prevent them from recurring, we should use RCA for its fundamental purpose – that is, the IDENTIFICATION of the root cause of the problem, rather than spending obscene amounts of time, effort, and resources applying solutions to mere symptoms of the problem.
RCA AND ITS PROMISE
Root Cause Analysis may seem and sound like rocket science but it really isn’t a vicious undertaking. Quite the opposite, RCA gives anyone the certainty that a problem can be solved by employing simple tools for the identification of its root cause. Also, practically anyone in the organization can facilitate an RCA initiative, from executives belonging to the C-suite down to the entry-level staff.
WHAT RCA IS NOT
Root Cause Analysis means what it is; it is ANALYSIS, meaning “to break down or divide a complex whole into smaller parts.” RCA is an application of techniques that enables you to look beneath the surface, explore the causal pathways from the problem leading to its true root cause/s. RCA does not guarantee that the problem will be solved. After all, it is possible to accurately determine the true root cause of a problem but invest in and apply the wrong solution.
To know more about RCA and our courses under the General Quality Track, please send us a message today or call us at (632) 551 – 2451!