Facing problems is a fact of life. And it can get trickier if you’re running…
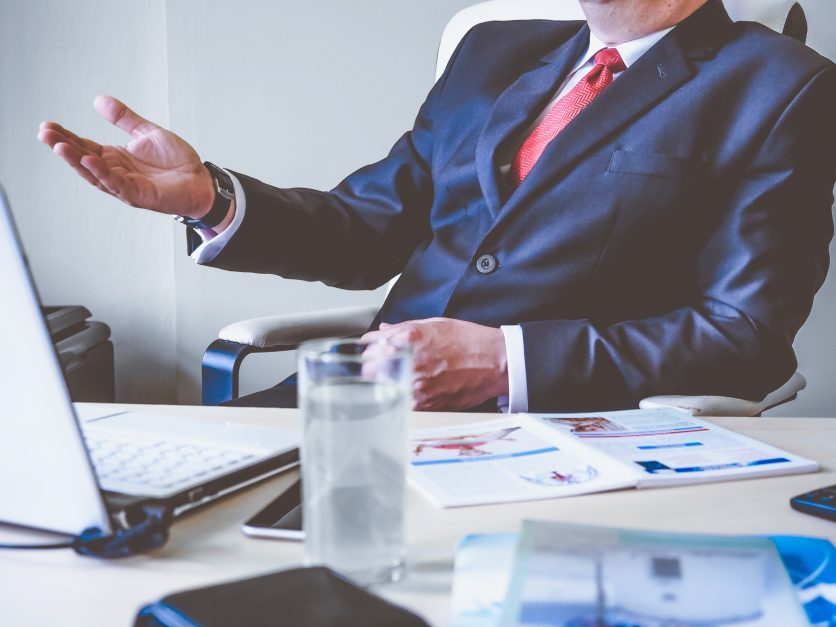
Kaizen: The Challenge of Continuous Improvement
Within the overlapping spheres of Total Quality Management and Lean Manufacturing, one Japanese word continues to raise consciousness among quality professionals of Western orientations: “Kaizen.” The concept of Kaizen, which direct translation means “continuous improvement, was first coined and introduced by the Japanese manufacturing industry in the 1950s to the 1960s.
For many, Kaizen is a way of life. It’s not merely a “rule” that should be enforced at every level in the organization. Let’s learn more about it here!
GOALS OF A KAIZEN ORGANIZATION
The Goals of a Kaizen Organization are four-fold, namely:
- To build a profitable, stable, and sustainable organization
- To increase efficiency by eliminating wastes in the process concerning time, money, materials, and other resources.
- To adopt a proactive stance in improving processes and systems, however incremental, before problems come rather than applying corrective actions.
- To foster the culture of quality
KEY CONCEPTS IN KAIZEN
- Evolution, Not Revolution. In Kaizen, it’s always better to create small continual changes than one big disruptive change. Incremental changes are more effective and sustainable than improving one thing in one swoop.
- “Every” is the Operative Word. Everyone participates in the quality initiative and every aspect of the business is a candidate for improvement. Every employee is encouraged to provide feedback and forward suggestions on how to improve their area of work.
- Ownership Mentality. Every employee has his or her hand on the rudder of the company. He or she is part of the cogwheels that run the organization. They are the experts on the job and knows the ins-and-outs of the company: This kind of ownership mentality encourages commitment from all employees, and they feel more fulfilled in their daily jobs.
- Use of Quality Tools. Kaizen teams are known for employing quality tools (both quantitative and qualitative) like the flowcharts, check sheets, control charts, scatter diagrams, histograms to assess and review their processes and systems and find ways to improve them.
- Quality Circles. A quality circle is akin to a Kaizen team. A quality circle is a team or a group of people meeting to analyze and review work practices with the aim of improving their processes, policies, and systems. Borrowed from engineering and manufacturing companies, quality circles promote a cooperative and collaborative atmosphere for discussing and suggesting improvements.
COMMON PITFALLS IN KAIZEN
Despite the good promises of Kaizen, there are instances when the methodology becomes unsuccessful. Here are some cases where the employment of Kaizen principles can do more harm than good to an organization:
- Using Kaizen to complement an existing failing system, without rectifying the erroneous structures first.
- Training for Kaizen among employees is insufficient.
- There is no management support for a Kaizen initiative.
- Employees perceive Kaizen as a chore, rather than a way of life in the organization. They find no meaning in it, or perhaps its purpose wasn’t communicated to them.
Like any quality methodology, the fruits of Kaizen will be sweeter if every person in the organization believes and partakes in its success. The proper integration of Kaizen into your processes, and people’s way of thinking will ensure better results for any quality management initiative.